We were able to reduce energy consumption for each fan by 50–70%. Garage exhaust fan run times were reduced by 99%.

Asset Facts
Date Built 1972
No. of Rooms 1000
Asset Type Hotel and Garage
Project Facts
Annual Energy Savings 1,088,326 kWh
Annual Cost Savings $110,671
Gross Investment $218,665
Rebates $49,760
Rebates as & of Total Project Cost 23
Net Investment $168,905
Net Payback 1.52 years
ROI: 66%
Energy Savings 7%
Energy consumption cut 50–70% for each fan
Garage exhaust fan runtimes reduced by 99%
Energy usage reduced by over one million kWh per year
Annual energy savings exceed $110,000.
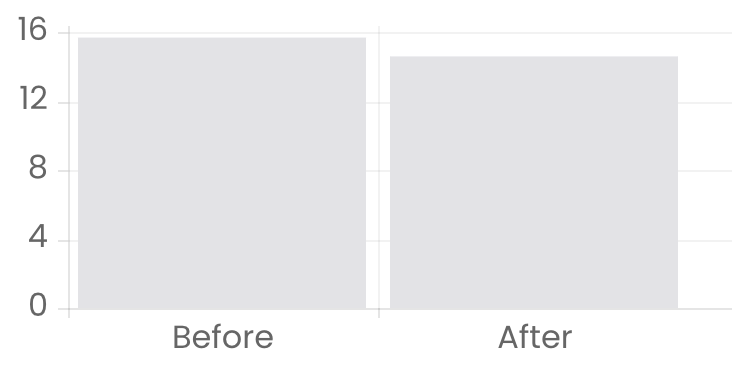
Millions of kWh Annually
Challenge
25 AHUs (Air Handling Units) were used to condition all common areas (lobbies, hallways, conference rooms) of a 1,000-room Hyatt hotel in Texas. Units ran 24/7 at full speed with no correlation to actual conditions, creating a wasteful, constant airflow.
Several garage fans also ran full speed, 24/7, without regard to either occupancy or actual carbon monoxide (CO) levels, which the fans were designed to reduce.
Our Solution
Upgraded HVAC and garage exhaust fans with high-efficiency motors and advanced controls to match energy consumption with actual demand. All air handling unit fan motors had variable frequency drives (VFDs) installed on them to convert the constant flow system to variable flow.
Measured airflow rates and adjusted CFM rates to match air flow with heating and cooling demands of each space served
Installed CO sensors and on/off controls on all garage fans
Converted all 25 AHU motors to high-efficiency models, extending their lives by reducing wear and tear
Tied space temperature monitoring into an overall building management system
Installed advanced, programmable digital thermostats
Created charge-back capability for AHUs in meeting spaces.